
Stop! Focus on all projects or activities you are currently involved with, or may be planning. Stay reminded that today it is pretty much an industry standard to perform Job Safety Analyses (JSA) to identify and mitigate potential safety hazards prior to starting all projects. If you have done so, have you recognized all potential implications that might result from identified or not-yet identified changed conditions within, 1) current in-progress activities/projects, 2) mitigations developed in response to previously identified changed conditions, or 3) anticipated planned operations that are intended to follow completion of planned activities/projects; regardless of size or complexity? Unanticipated changes can potentially have significant negative safety and/or financial implications . So, has sufficient review been invested into the planned resultant conditions or operations following completion of your projects or tasks?
Every task or operation requires planning at some level for all phases to continuously maintain safe conditions for workers and involved/affected systems throughout. Activity or project planning can often be a long and involved process, where we often expect that safety is one of the final considerations to be totally defined. Will the planned mitigations for identified hazards result in changed conditions that must also be risk assessed as well? Do your planned mitigations introduce additional new and different risks potentially affecting personnel health and safety, the environment, or equipment integrity? Irrespective of the project/task scope, it is important to continuously monitor activities for changes, because conditions are often dynamic and could potentially impact worker safety or subsequent facility operations unexpectedly. Even when you risk assess and plan your projects/activities properly, there will always be aspects that result in possibly unrelated risks that are controlled by others unknown to you (potential simultaneous activities). For that reason, monitoring and planning for changed conditions should never end until the project is complete.
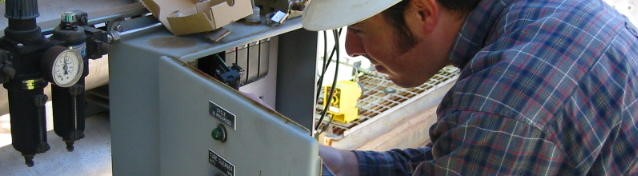
So, how should someone best avoid complications resulting from changed conditions? First a fairly rigorous and organized planning process is very helpful. That process will evaluate current and future intended conditions on site and in surrounding areas, then scope out how to achieve the desired goals. It is smart to start involving the entire team in the planning process as early as possible to develop and finalize the planned scope of activities based on input from all your resources. Including the entire team, most senior to least senior provides all members the ability to share their, many times unique knowledge, with the team. Often, lesser experience workers are the ones who actually perform many tasks giving them a unique understanding of the potential hazards. That unique understanding can be drawn out during team discussions which can then be documented during the Job Safety Analysis development process to benefit the project. Use all your resources to make all projects as safe as they can possibly be, then work smart. Remember, a common root cause for accidents is a poorly managed change.
To ensure that changes do not take place without a systematic procedure to examine their impacts and manage any associated risks, you need a process.
A basic management of change process involves:
- Understanding Changes. Fully explore and understand conditions to describe and define what changes have been identified. Many times, a project will be designed to specifically implement desired changes. Any changes must then be understood and risk assessed to identify all the potential hazards. It is preferrable to involve the entire team in the Job Safety Analysis process then complete and fully vet the results prior to the start of projects.
- Carefully Plan Changes. Once there is a comprehensive understanding of the changes, they must be risk assessed to identify all the potential hazards. Mitigations must then be designed to engineer out and eliminate all the hazards to the extent possible.
- Communicate Changes. A key element to the success of any JSA/management of change (MOC) andrisk mitigation process is communication of the detected risks, agreed upon changes, and mitigations to all involved individuals to minimize the safety risks.
- Implement Planned Changes. It is important that changes get implemented exactly as they were agreed upon in advance. Deviations will likely introduce additional risks.
- Continue monitoring for consequential changes in conditions. The need for monitoring does not end until the project is completed. That is an integral and necessary part of the process.
- Document Details and Results. This confirms that the agreed upon plan was completed as defined and provides as basis to evaluate any lessons learned.
Changes that should require assessment and management of risks are as follows:
- Administrative – changes to policies, procedures, business processes which potentially have health and safety or environmental impacts.
- Organizational/Personnel - changes in staffing, authority level, employment terms and conditions.
- Technical – changes to existing equipment, design practices, operating conditions (outside allowed limits).
- Replacement in Kind – replacement with something that is essentially the same should not normally be subject to MOC, but still should have a JSA conducted to inform the team performing the work about related safety concerns.
To support continuous improvement, teams need to always remain vigilant of their responses to identified risks, to recognize if their responses themselves initiate consequential risks that may require mitigation. The Job Safety Analysis provides a great tool to identify and mitigate risks as projects progress.
JSAs are a useful tool that can aid the identification of changed conditions, which can help a work team to develop and agree on revised mitigations at their worksite throughout the project/activity. Those mitigation revisions can then be immediately documented with a MOC annotation right on the Job Safety Analysis. That facilitates helping everybody to complete their tasks safely, in an efficient manner. Performing these JSA/MOC steps during reviews helps to keep all team members engaged in thinking about their current work tasks and helps eliminate potential hazards. A JSA worksheet provides employers so much value so inexpensively, it’s difficult to understand why anyone would not use a Job Safety Analysis for every project task.
Go to jsabuilder.com and test the referenced JSA software for free, and help your team work safely and go home at the end of each work day without harm. Follow us on LinkedIn and Twitter @JSABuilder, where we tweet about Health and Safety, post Safety tips, and provide updates on current Health and Safety topics. We also highly recommend that you try one of our other top safety tools at www.LOTOBuilder.com today, where our database-driven Lockout Tagout tool is currently available for a FREE 30-day trial, which will allow you to manage your lock out tag out program from start to finish. Easily enter your workers, equipment and procedures to build an entire LOTO program. Save time and money using LOTOBuilder and help your workers to work safe.
Note: images, links, brands discussed or displayed in this article are not endorsements or recommendations. They are for illustration of various products and types of products. JSABuilder does not recommend products, does not endorse, or express any opinion as to the applicability to any given use case or job hazard. Again, consult your safety professional to obtain authoritative opinions on applicability, selection and fitting of all the various types of PPE, then work smart and safe.